製造業以外にも応用できる?5S活動の実際
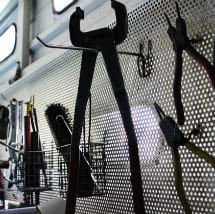
作成日:2017/04/12
トヨタ生産方式のなかで生まれた5S
かつて世界の市場を席巻した日本の製造業の強みは、いわゆる「トヨタ生産方式」と呼ばれるものでした。「自働化」と「ジャスト・イン・タイム」を考え方の根本においたこの生産方式は、後にマサチューセッツ工科大学で研究され、「リーン生産方式」として再体系化が図られ、「今や、世界中で知られ、研究されている『つくり方』」(トヨタ自動車HPより引用)となったわけです。その中でもっとも重要な要素のひとつとされているのが、「生産現場の『ムダ・ムラ・ムリ』を徹底的になくし、良いものだけを効率良く造る」(同上)という考え方とその実践です。
たとえば「五回の『なぜ』を自問自答することによって、ものごとの因果関係とか、その裏にひそむ本当の原因」(『トヨタ生産方式』/大野 耐一 元副社長 著)を突き止めることができるという「なぜなぜ5回」や、「後工程が前工程に部品を調達しに行く際に、何が使われたかを相手に伝える道具として、『かんばん(注:現在は電子的なeかんばん)』を利用」(トヨタ自動車HPより引用)する「かんばん方式」は、この考え方に基づく有名な方法です。
そして、それらと並んで不可欠とされるのが「整理、整頓、清掃、清潔、しつけ」の頭文字をとった「5S」、あるいは「5S運動」と呼ばれる業務改善手法です。
☆あわせて読みたい
『【PMOとは】PMとの違い(仕事内容・意味・職種)と向いている人、業務に必要な資格・スキルセットを解説!』
『【フリーコンサル PMO】年収は?必要なスキルや資格は?つまらない?メリット・デメリットも解説』
5S活動の定義と効用
5Sはもともと「整理、整頓、清掃」の3Sという業務改善の取り組みに「清潔」を加えた4Sを経て完成されたものです。
生産現場における5Sの具体的な活動は次のように定義できます。
1.整理=使わないものは片付けるか捨てる
2.整頓=決められたものを決められたところにきちんと置く
3.清掃=職場をきれいに清掃しておく、作業者自身も汚れのないようにする
4.清潔=清掃した状態を保ち、常に汚さないようにする
5.しつけ=上記の決められたことを確実に守り自然に出来るようにする
では、なぜこの運動が業務改善に有効なのでしょうか。その理由としては下記の5点があげられます。
1.「整理」したものの残りは業務に必要なものばかり
2.「整頓」することで、必要なものが常に定位置に置かれ、探しやすくなる
3.「清掃」によって、機械や現場などでの問題点が見つけやすくなる
4.「清潔」を意識し続けることによって「整理、整頓、清掃」の状態が維持できる
5.「しつけ」を徹底することで、職場の一体感を醸成し、自然体的な5Sが習慣化される
一見、ごく当たり前のことに思えますが、これら5S活動によって業務改善が実現でき、生産現場の効率化、ひいては企業の利益増につながることは、現在のトヨタが物語っていると言えます。また、副次的なメリットとして、従業員の意識向上や生産現場での安全性向上が図れるというものもあります。
逆に、整理・整頓を徹底しなかったある生産現場では、1時間の作業のうち大半の時間を工具やマニュアル探しに費やしていたという話もあります。探す時間のムダが生産性の向上を妨げていたわけです。
☆あわせて読みたい
『フリーランス人材の悩みとは?業務委託の雇用形態とメリットデメリットを解説』
5S活動が失敗するケースとは
業務改善に効果的な5Sですが、導入の方法を間違えるとまったく機能せずに失敗に終わることもあります。一般に、5S活動が失敗する要因は下記の3点であるとされています。
1.トップの思いつきで始まり、手順や社内意識の統一がなされていない
5Sは、トップダウンで開始したとしても、最後は社員自らが考えて動かなければならない「ボトムアップ」の活動です。仕組みの確立や社内のコンセンサス統一がなされていなければ、ただの「片付け」に終始してしまいます。
2.点の活動で終わる
5Sは「継続的活動」なので、継続することが重要です。5Sの目的を全社員に明示し、活動を維持する仕組みを作らなければ、5Sは瞬間的な行動で終わってしまいます。
3.リーダーが存在しない
5S推進者の業務生産性に対する問題意識が低いと、活動は形骸化していきます。たとえば「ちゃんと工具をしまっておけ」「身だしなみに気をつけろ」などの恣意的な指示では、従業員も「何のためにそうするのか」を理解することはできません。
生産性向上のための手段である5S活動が目的と化してしまうと、従業員に「やらされ感」が蔓延し、かえってモチベーションが下がり、業務効率化どころではありません。マネジメント層や5Sリーダーは、「何のために行なう活動なのか」を従業員に理解させる努力が常に必要なのです。
5Sはほとんどの業種に応用できる
一般に5S活動は、生産現場での業務改善方法と考えられがちですが、実は意外と他の業種にも応用が効きます。身近なところでは、デスクワーク部門における必要書類と不要書類の分別による書類探しの時間短縮、引出しの整理やテープなど共用事務用品の定位置への配置と返却による備品探しの時間短縮に効果があります。さらには常にパソコン内のデータを整理し、不要なファイルを削除することでも「検索」という作業が大幅に楽になります。
たとえばリコージャパン株式会社は、オフィスでの5S運動に積極的に取り組んでおり、「整理整頓されたオフィスで気持ちよく働くことはESの向上はもちろんの事、オフィスに来社されたお客様の心象もよくなりCS向上にも繋がっていきます」(リコージャパンHPより引用)としています。
また小売業の場合では、バックヤードの在庫を常に整理・整頓して品揃えの過不足を把握することや、店舗の清掃を徹底することでCSの向上にもつながります。5Sとは製造業のためだけの業務改善運動ではなく、小売・サービス業、流通業、物流業、医療機関などありとあらゆる業種に応用可能な手法なのです。
公益財団法人 日本生産性本部の発表によれば、2012年の日本の製造業の生産性は、OECD加盟国中第7位だったそうです。1995年に第1位を獲得したことに比べればやや後退した感があるものの、主要先進7カ国で比べれば、米国に次いで第2位であり、依然高い水準を誇っているといえます。
米国の製造業の生産性が高いのは、工場の海外移転などが進み「生産性や収益性に優れた企業のウエイトが高くなっている」(日本生産性本部『OECD諸国の労働生産性の国際比較 2016年版』より引用)ためであり、実質的には日本の製造業の方が生産性が高いということができます。このことからも、5Sやカイゼンといった日本的なボトムアップ型の業務改善手法は、生産性の向上に大きな効果をもたらしているということができるでしょう。
一見、極めて当たり前の活動に思えるものの、継続により大きな効果が期待できる5S。チームで働く際取り入れてみることで、これまでにない新しい変化が生まれるかもしれません。
(株式会社みらいワークス Freeconsultant.jp編集部)
◇こちらの記事もオススメです◇